hot end temp plateaus before reaching target temp
this is picking up from this post https://forum.repetier.com/discussion/7749/v2-firmware-endstop-configuration#latest
I run M303 S200 C3 but the firmware errors out at 120
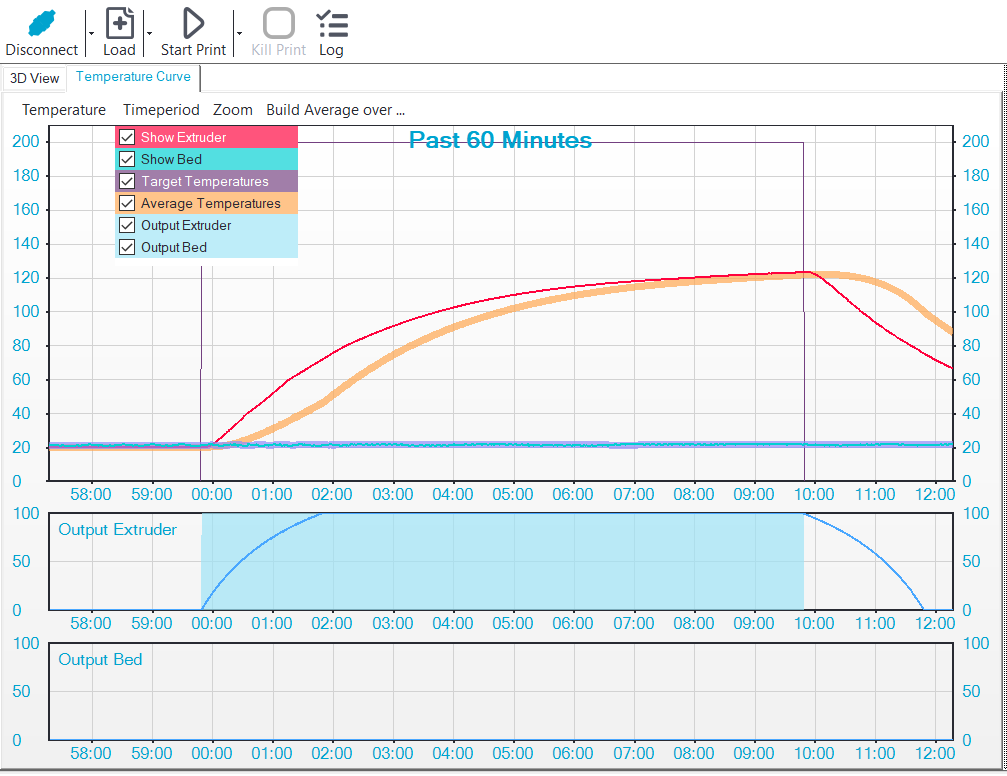
configuration.h:
I run M303 S200 C3 but the firmware errors out at 120
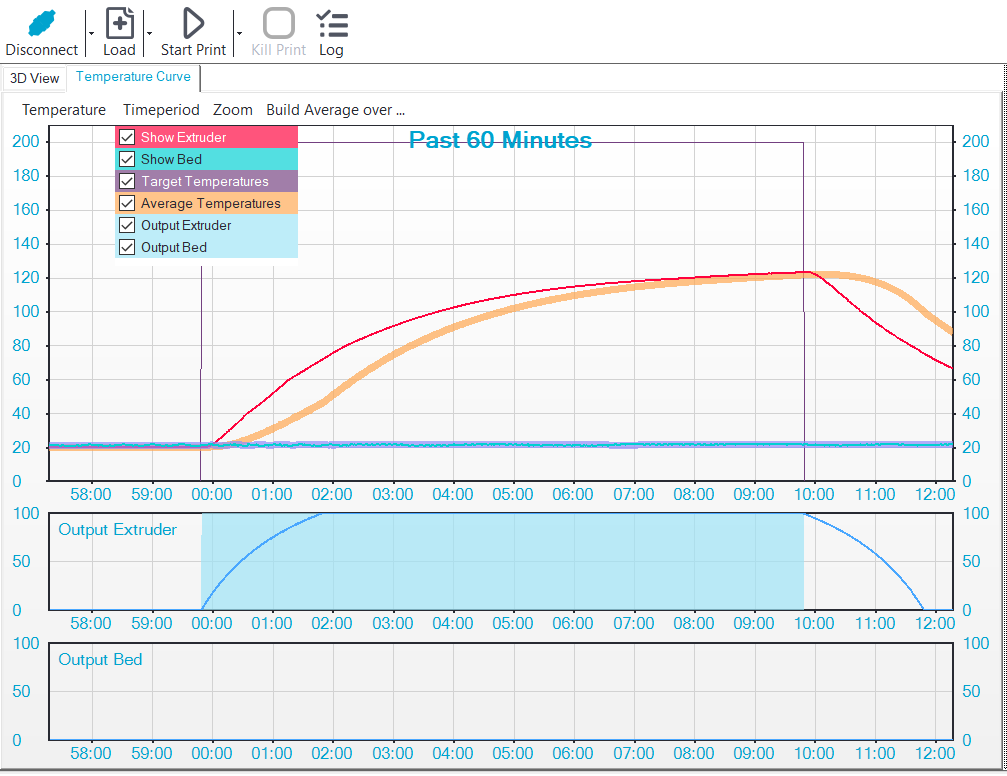
configuration.h:
#define NUM_HEATERS 2
#define HEATERS \
{ &HeaterExtruder1, &HeatedBed1 }
configurationio.h:
configurationio.h:
IO_PWM_HARDWARE(PWMExtruder1_12V, HEATER_0_PIN, 1000)
IO_PWM_HARDWARE(PWMBed1, HEATER_1_PIN, 1000)
HEAT_MANAGER_PID(HeatedBed1, 'B', 0, TempBed1, PWMBed1, 120, 255, 1000, 10, 300000, 190.05, 37.12, 648.72, 80, 255, false)
HEAT_MANAGER_PID(HeaterExtruder1, 'E', 0, TempExt1, PWMExtruder1, 270, 255, 1000, 20, 20000, 20.25, 1.13, 90.44, 40, 255, false)
rumba32.h
TOOL_EXTRUDER(ToolExtruder1, 0, -13, 0, HeaterExtruder1, E1Motor, 1.75, 500, 5, 30, 5000, 177, "M117 Extruder 1", "", &Fan1PWM)
TOOL_EXTRUDER(ToolExtruder2, 0, 13, 0, HeaterExtruder1, E2Motor, 1.75, 500, 5, 30, 5000, 177, "M117 Extruder 2", "", &Fan1PWM)
rumba32.h
Comments
IO_TEMP_TABLE_NTC(TempTableEpcos, Epcos_B57560G0107F000)
configuration.io.h:
but in variants.h
#define TEMP_0_PIN static_cast<int>(PC_4) // T0 pin is listed as PC4 which is pin 36 not pin 5
should I change TEMP_0_PIN to pin 36, TEMP_2_PIN to pin 35, and TEMP_1_PIN to pin 32?