problem with endstops
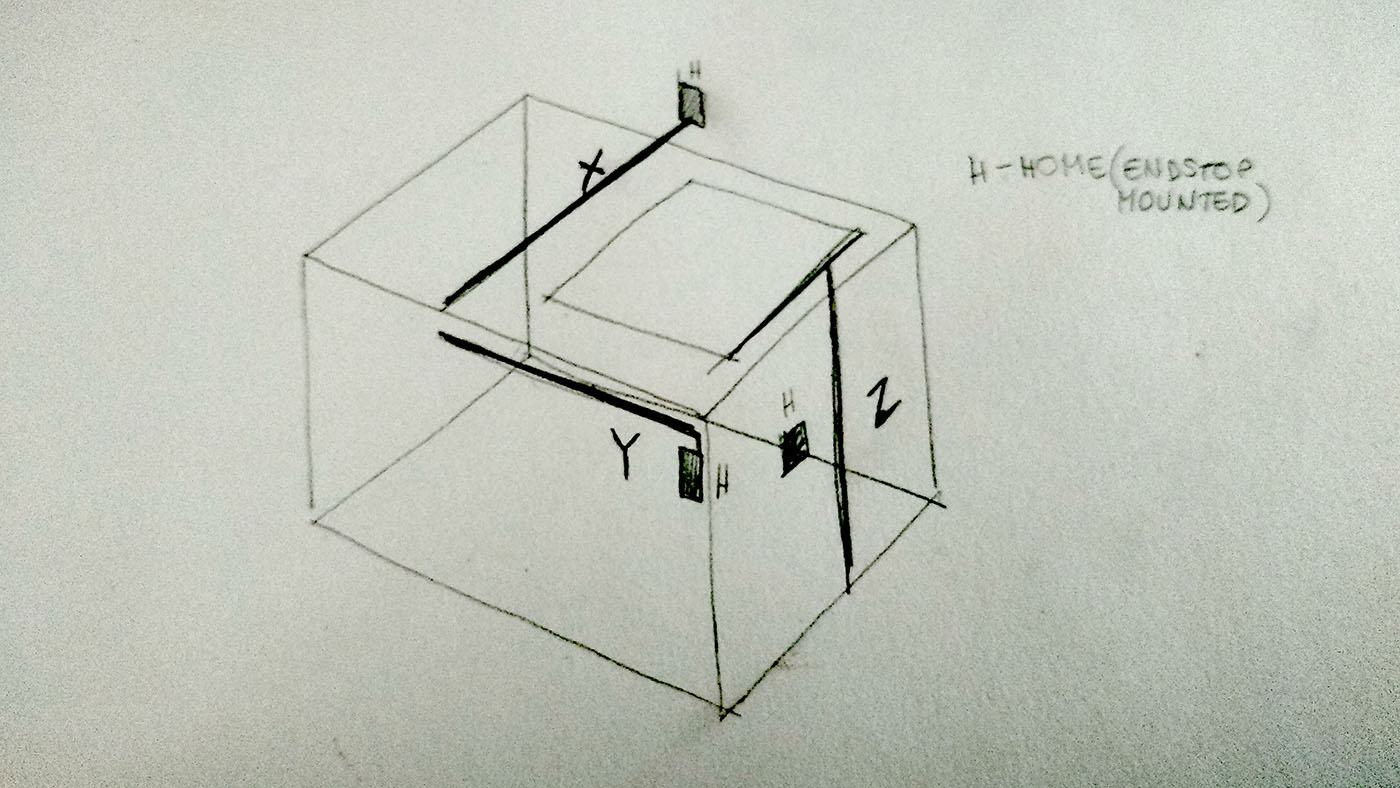
I'm building a custom 3d printer using arduino 2560 and ramps 1.4. For X axis I use nema 17 motor with a TB 6600 driver, Y nema 23 also with TB 6600 driver and for Z axis and extruder motor nema 17 and A4899 drivers. I'm having trouble configuring the endstops. I have instaled three optical endstops blasini optical endstops. I've checked everything multiple times and the electronics are connected corectly. Tried everything. and combined almost everything in the mechanics part of the repetier firmware configuration tools and still have problems.
Comments
You did not tell what the problem is. Use M119 to see first if all endstops trigger and if they are named correctly min/max. Main error is either having defined end stop type min/max or having homing direction inverted because your direction in inverted you you try to fix one error with additional errors.
Also not that the felix printers move bed towards you which is y max homing so you need y max endstop for that direction.
If I did understand you correctly, I should change the connector on the board to Y max position? And then change the direction of the homing in the firmware, or not?
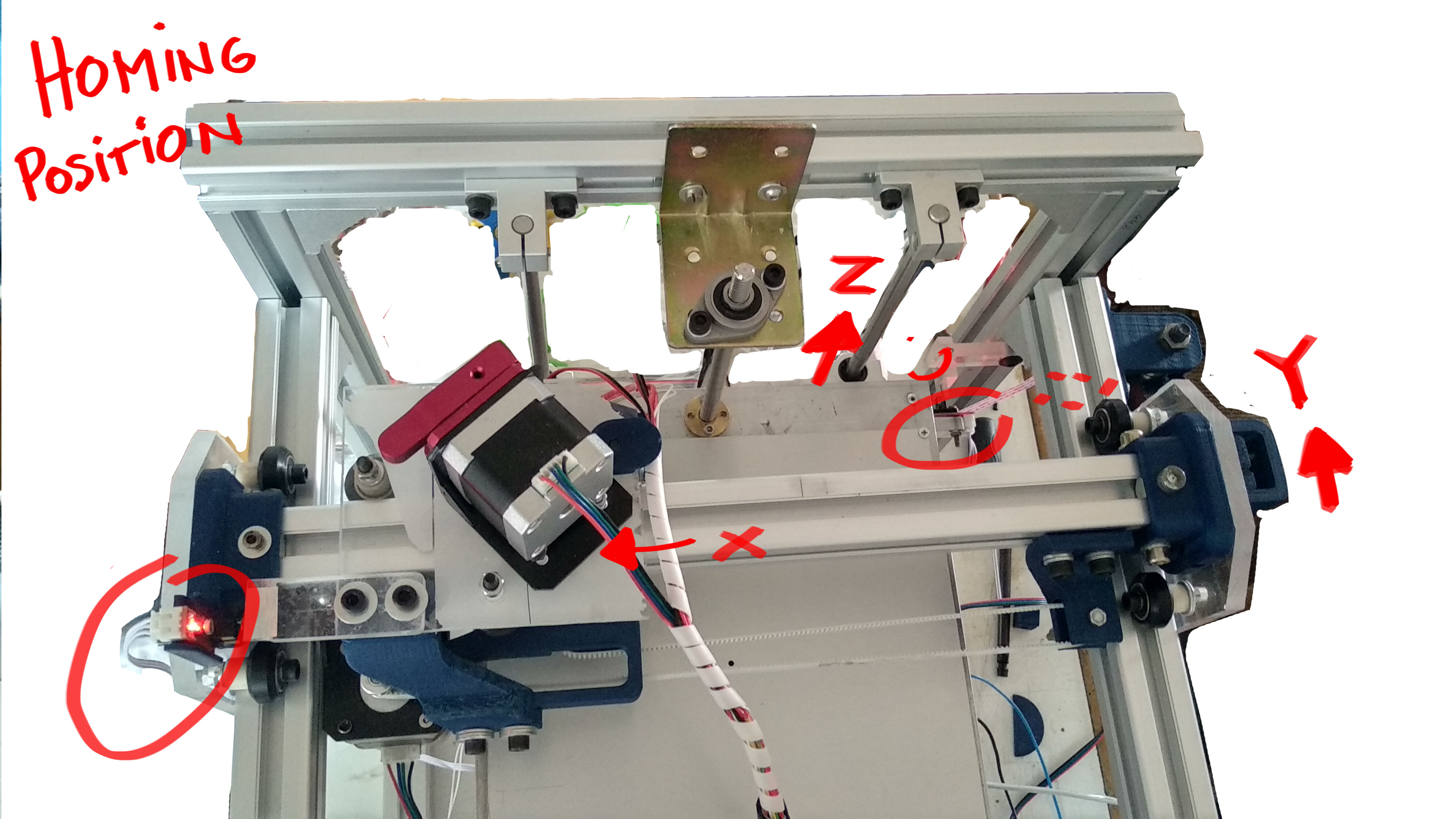
what the configuration looks likeX endstop left is x min endstop.
So yes Y should have homing direction 1 and define y max endstop while x and z have homing direction -1 and min end stops.
It now homes incremental, it works. When homed, the M119 command sent to the printer it says: 17:33:30.110 : endstops hit: x_min:L y_max:L z_min:H. Is that the way it should display? And I've experienced this behaviour:
cannot move manually in the repetier host the axis in the opposite direction. Also if I turn off the power and disconnect, and manually by hand move the Y axis and again turn on the printer and connect, and home the Y axis it does not recognize the endstop. Of these two problems, the second one is the more serious. What that could be?
M119 z min is triggered. Would be ok if nozzle hits bed.
The move increments - are they always the same distance or different distances?
Also check in eeprom what steps per mm and xyz length are. Wrong values here can lead to not doing full move. Values are only set on first upload then the stored values are used, so it is easy to have different values in eeprom.
M502
M500
would copy the values from config to eeprom again. Or adjust them individually in eeprom editor.
Move increments are always the same now
Steps per mm are the same as are the length, done the M502 M500 commands.
I think I should change the position of the X endstop, moving it to the side where the Y endstops are would be better for machine control, right now when I run the dry test g code (which is made n repetier, only without the start procedure, and G92 X0 Y0 Z0 ) Y works the way it should but X is moving in the direction where the endstop is and it should be moving the opposite direction. The Z was moving the wrong direction, I've inverted the direction in the firmware and now it is working properly.
Besides that there is one more problem I've encountered- extruder stepper is not working.
Tried swapping the A4988 driver with the one from the Felix 3d printer that is working and also nothing happened.
Turned on the hot end, also nothing (I thought maybe it was due to cold extrusion safety feature) what would be the test g code command to try
makes cold extrusion possible. Check in eeprom if all parameters are set correctly (steps, jerk, acceleration).
Also check if extruder blocks when enabling printer. Drivers differ if enable pin needs high or low. At start it should be unpowered so you should be able to rotate motor easily. When extruding it is enabled and be hard to move. If enable is wrong it will be disabled when moving so nothing happens.