After PID tuning extruder still overshoots on temp.
My Diamond hot end clogged so I switched to a V6 bowden fed single nozzle. While bridging a large area my heater (same that was in the diamond) struggled to stay at 230 C and dropped to 226 before I slowed down the cooling fan. It slowly heated up to 230 and after the bridging was done it continued to climb to 251 and trigger decoupling error despite full fan and increased feedrate. Same thing before and after PID tuning ( M303 E0 S230 C6) and entering the new values. Any ideas how to fix this overshoot?

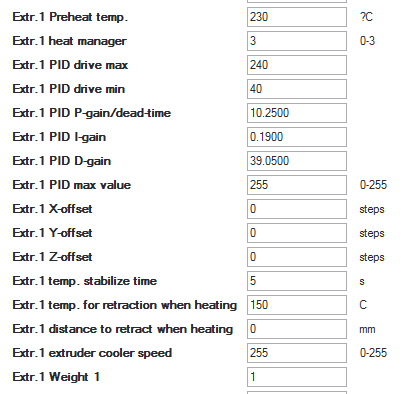
Comments
For the decoupling problem you can increase the variance of course, bat that is not the real problem you want to solve I guess.
Searching for PID_CONTROL_RANGE I did not find any line changing the set value to limits. But you need to reupload the firmware.