Could a Delta Printer Like This Work?
I've been 3D printing for a few years now with a standard XYZ printer, but I've always loved the Delta/Rostock look, and the mechanics of them. The company I work for has done a small amount of work with some delta style industrial robots, but unlike the rostock printers, they don't operate on verticle slides. They operate much like the image below. I would love to build a 3D printer in this style! However, since the up/down motion of each arm is not linear (like a regular Rostock would be), some math to calculate position correctly would obviously have to change.
I don't know for sure, but I believe the firmware would be responsible for determining position (not Repetier, Slic3r, etc.). Does anyone know this stuff well enough to say how this could be done? Would it be a major undertaking where the entire firmware needs to be written from scratch, or would it just be a matter of changing a few things here and there to make it work? Thanks!
I don't know for sure, but I believe the firmware would be responsible for determining position (not Repetier, Slic3r, etc.). Does anyone know this stuff well enough to say how this could be done? Would it be a major undertaking where the entire firmware needs to be written from scratch, or would it just be a matter of changing a few things here and there to make it work? Thanks!
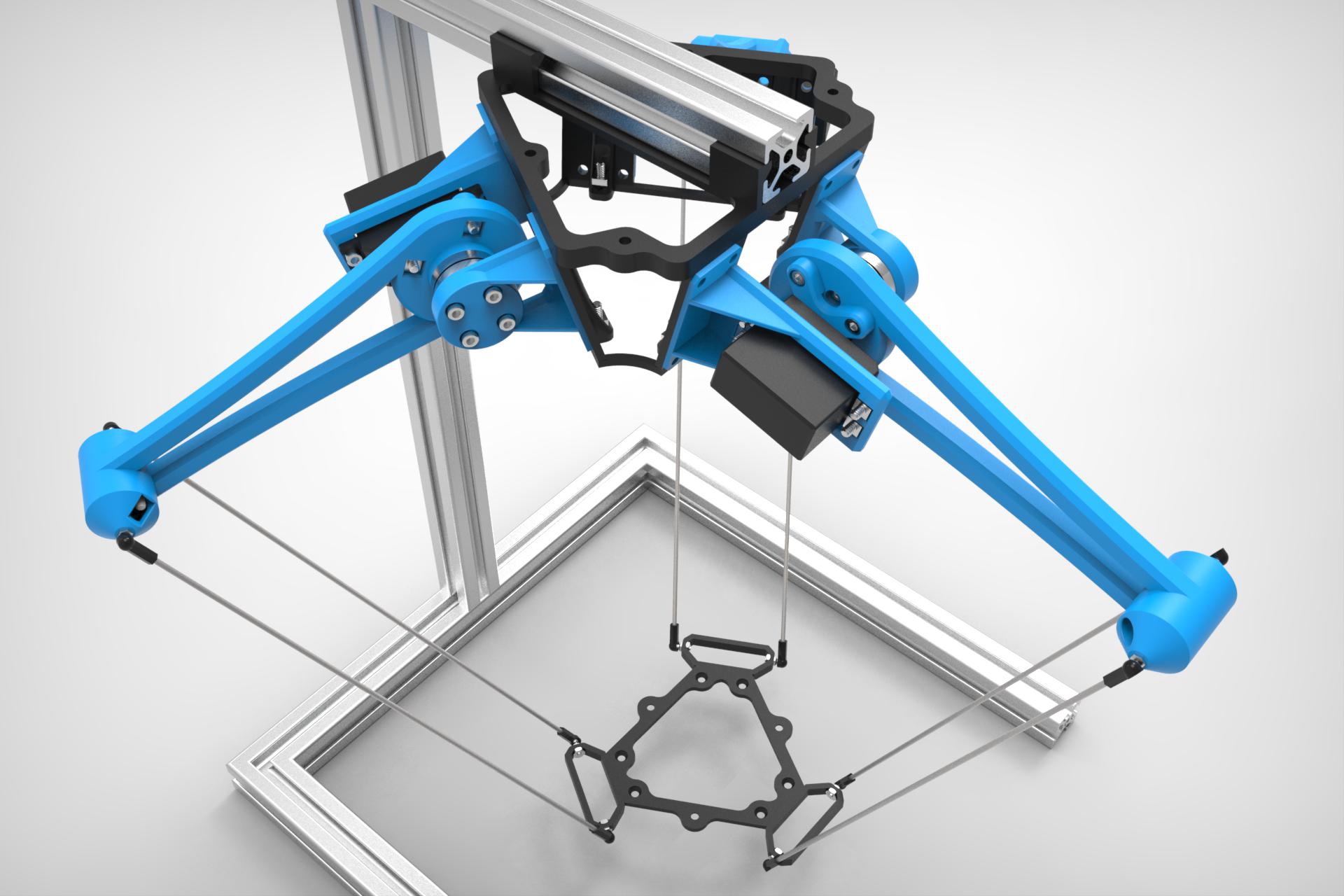
Comments
Main problem is speed I guess. Original design only requires 3-4 sqrt operations to solve the transformation. Here I fear you are requiring the even slower sin/cos/tan math.
Next problem is resolution. This design changes resolution over height and the top angle drive needs a really high precision to get good prints and not to forget a very stiff top to not put vibrations into the print.
So while delta design is already demanding that notches it one more level in complexity.
I have looked a tiny bit into the kinematics for these types of delta robots, and I believe you are 100% correct, it requires sin/cos vs the basic sqrt. Because I have minimal Arduino experience, I have no idea how much slower this would be.
Definitely right again on the precision. I would intend to have steppers driving the arms via a gear connection. Probably around a 4:1 ratio, maybe higher if required. I have not looked into any design constraints yet, but ideally none of the upper arms would be working too close to their extremes. Stiff mount would absolutely be required. Much stiffer than what is in that example picture.
Regarding resolution you want around 100 steps per mm at the worst position, so 4:1 is not enough I think. Maybe 16:1 for a small delta. But that is without any calculations.
But I guess you see where the problem is. Ratio 50:1 without any backlash and precise positioning is the main problem for quality you will face here.